Introduction
Electric power generation plants must ensure that sufficient electricity is supplied to customers at all times. Preventive maintenance of the power generation equipment is, therefore, critical for maintaining reliability as well as reducing overall operational costs.
Conventional fuels like coal, and natural gas are still the most common types used in power generation facilities around the world, complemented by nuclear, diesel, and renewables like hydroelectric, wind, and geothermal power.
A central component in wind energy converters and hydroelectric power stations is the turbine engine, which not only works with oil and gas but also with wind and water flow. Since turbine engines use lubricants, they must be inspected regularly.
Other types of equipment used in power plants that are important to regularly inspect include:
- Steam engines
- Hydraulic pump engines
- Diesel engines
- Gear box engines
- Gas turbines
All these devices use hydraulic oil, making it important to monitor the cleanliness (particulate inspection) of the hydraulic oil to keep the equipment running smoothly.
The conventional method used to inspect oils for particulates is a laser-based automatic particle counter (APC). However, APC measurements do not provide any details about the size of the particles or whether they are reflecting (e.g., metal) or non-reflecting (e.g., fibers). Also, laser-based particle counters often overlook transparent particles or overcount due to bubbles in the liquid.
Improved Particle Inspection with the OLYMPUS CIX100 System
For a comprehensive overview of particulates in an oil sample, automatic microscopic particle analysis inspection systems, such as the CIX100 technical cleanliness inspector, offer advantages over APCs, such as:
- High image resolution (0.63 μm/pixel using a 10x lens) enables the system to detect particles as small as 2.5 μm with an inspection time of under 10 minutes.
- Innovative and patented illumination system automatically detects reflective (metallic) and nonreflective particles in a single scan, saving time. No user adjustments are required, helping ensure measurement comparability between users and CIX100 systems.
- Reduced risk of contamination and handling errors—simply insert the specimen in the microscope, and the rest of the process is automated.
- Particle morphology and height measurement data.
- Easy, traceable calibration.
- Compliant to international technical cleanliness standards for oil inspection, including ISO 4406, ISO 4407, NAS 1638, DIN 51455, and SAE AS4059.
The Technical Cleanliness Workflow
Below, we lay out the basic steps of the technical cleanliness inspection process. In just 5 simple steps, users can quickly generate reliable inspection data.
Step 1: Collect an oil sample from the equipment
Step 2: The oil is passed through a vacuum filter machine, and the filter membrane collects any particles.
![]() Place a 47 mm (1.85 in.) filter membrane on the filtration apparatus | ![]() Pour the oil into a beaker |
Step 3: Weigh the filter membrane after it dries.
![]() | The dried filter membrane containing any impurities is weighed using an analytical balance with an integrated wind shield. |
Step 4 and 5: The CIX100 system enables you to analyze the inspection results and then generate a professional, compliant report with one click.
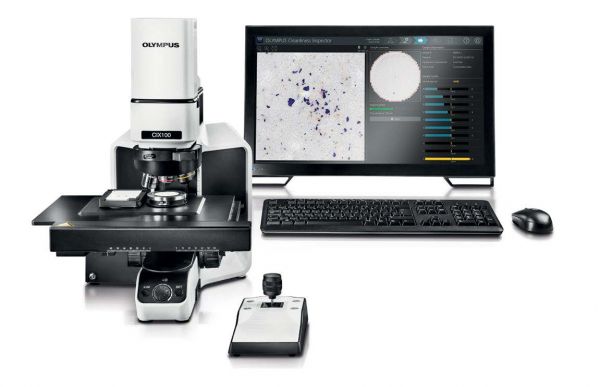
CIX100 system: automated, intuitive, step-by-step guidance and user rights management help ensure reliable data.