Headquartered in Ranshofen, Austria, HPI (High Performance Industrietechnik GmbH) develops, engineers, manufactures, and delivers turnkey equipment for the light metal industry. Metallurgical manufacturers typically use light metals, such as aluminum and magnesium, to produce light alloy-based products.
For one of its metallurgical customers, HPI innovated and developed an automated conductivity measurement system for nondestructive material testing. The conductivity measurement system that HPI built integrated our NORTEC™ 600 eddy current flaw detector for purposes of measuring and testing to meet quality demands.
The Challenge: A System That Validates Conductivity at Production Speeds
According to an article published in the Aluminium Times, HPI created the system to perform conductivity tests to assess the heat treatment state of aluminum plates. These plates are up to 4,200 mm (~14 ft) wide, up to 33,000 mm (~108 ft) long, and range from 1 mm to 210 mm (~0.039 in. to 8.3 in.) thick. These plates are transformed into semifinished aluminum and magnesium alloy products, which will be supplied to the aviation industry.
The metallurgical company needed the system for its new rolling mill complex comprising a cold rolling mill, hot rolling mill, and heat treatment of sheets. Its manufacturing process required a built-in reliable NDT inspection solution that would boost productivity while validating that its materials comply with internationally recognized standards.
The challenge for HPI was to develop a system that provides high-speed measurement of aluminum plate conductivity while maintaining a consistent testing performance.
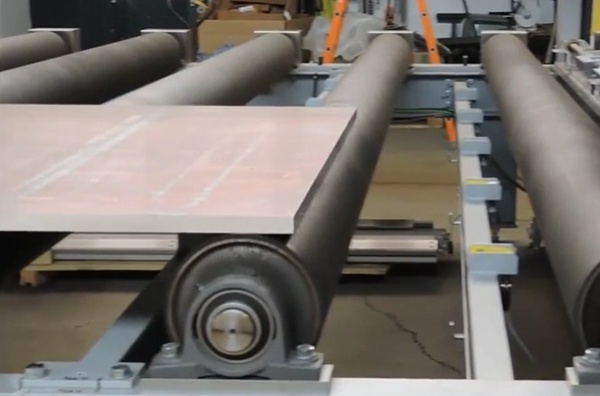
A large aluminum plate being transported on a production line roller table
Reasons Why Manufacturers Measure the Conductivity of Metals
Electrical conductivity measurement is used to determine how well a material allows electricity to flow through it, in other words, how well a material can conduct an electrical current. Such testing enables manufacturers to gather information about the composition of a substance. With this data, users can determine whether the material is suitable for its intended use.
Many industries incorporate conductivity testing into their quality control and manufacturing process. This is done to verify the authenticity of the metal’s structural integrity to be able to achieve desired durability and performance of the end product.
It is important to measure the conductivity of aluminum used in the construction of aircraft to know its capacity to discharge, assuring the ability of the aluminum to endure material stress caused by events such as lightning strikes. By detecting changes in the hardness of the alloy, conductivity testing can confirm if the material has been damaged by heat treatment, making it more brittle.
Aluminum’s Strengths, Weaknesses, and Typical Flaws
Aluminum has a density lower than those of other common metals. Steel, for example, is approximately one third denser than aluminum. Because it is lightweight and strong, aluminum is ideal for aircraft manufacturing, with some sources estimating that a modern aircraft is 75–80% aluminum. Because they are mainly made from aluminum, aircraft can carry more weight and are more fuel efficient.
Another major benefit of aluminum alloys is their corrosion resistance, which increases an aircraft’s durability. Airplanes are constantly subject to the elements and climatic extremes, from freezing temperatures at high altitudes to precipitation including snow and rainstorms. Although aluminum has a high resistance to corrosion, it is a chemically active metal, so corrosion can occur.
Aluminum components are susceptible to various types of corrosion, including:
- Surface pitting
- Intergranular
- Exfoliation
- Stress-corrosion cracking (SCC)
- Fatigue cracking
- Fretting
Manufacturing processes, such as machining, forming, welding, or heat treatment, can leave stresses in aluminum sheets (and therefore aircraft parts). This residual stress can cause cracking in a corrosive environment when the threshold for stress corrosion is exceeded.
Advantages of Eddy Current NDT for Aviation and Aerospace Applications
Eddy current nondestructive testing (NDT) is a noncontact method for the inspection of metallic parts. It is widely used in the aviation and aerospace industries and other manufacturing and service environments that require inspection of thin metal for potential safety-related or quality-related problems.
Because eddy current testing (ECT) uses electromagnetic coupling and does not need to be in direct contact with the part, couplant is not required.
EDT can be used to perform:
- Surface inspection
- Subsurface inspection (typically 3–4 mm)
Eddy current technology benefits:
- Inspects through paint and coatings (no paint removal required)
- Minimal surface preparation (can inspect through dirt)
- Easy to use, so minimal training
- Provides rapid results, so it’s conducive to high-speed inspection and inspecting large parts
- Suitable for any material that conducts electricity, including the metals commonly used in aircraft, such as aluminum, stainless steel, and steel
How Eddy Current Testing Devices Work

(a) Alternating current injected into a coil creates a magnetic field (in blue). (b) When the coil is placed close to an electrically conductive material, an eddy current is induced in the material (in red). (c) Defects in the part disturb the path of the eddy current. This disturbance can be measured by the instrument.
When alternating electric current passes through one or more coils in an ECT probe assembly and that probe is close to a part made of conductive material, an alternating magnetic field is produced that induces eddy currents into the part. This magnetic field generates a coupling effect.
Discontinuities or property variations in the test part change the flow of the eddy current, which impacts the probe’s operating inductive reactance. Changes in the material’s thickness or defects such as cracks and corrosion in the inspected part are detected by the probe. These changes are reflected on the instrument’s screen in the signal’s phase and amplitude, which the operator then interprets.
HPI’s Solution for Conductivity Measurement of Aluminum Plates
This video shows a demonstration of the HPI solution, which is an automated system for high-speed conductivity measurement of aluminum plates. As you can see, the NORTEC 600 unit is integrated into the HPI system on a scanner that rapidly moves the ECT probe over the calibration station and over the aluminum plates after it is fed on rollers into the measurement station.
The measurement programs can be predefined for each plate, taking as reference the internationally recognized standards ASTME 1004-02, MIL STD1537C, EN2004-1 and AMS 2772F, and the customer-specific testing specifications of the aerospace industry.”
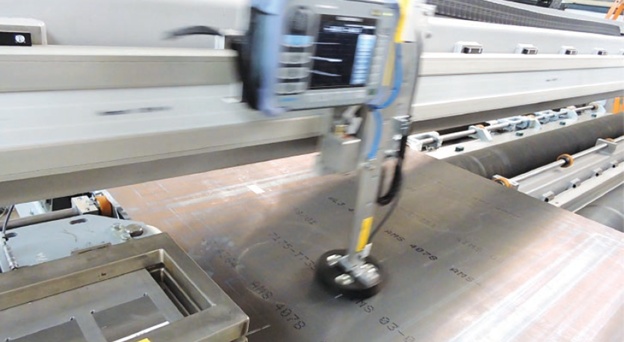
Conductivity measurement system for aluminum plates with an integrated NORTEC 600 ECT unit
HPI had used manual devices in the past for this kind of production line testing; however, with the increased speed and quality requirements, especially for the aviation and aerospace business, manual testing became obsolete. The combination of Olympus’ NORTEC 600 eddy current flaw detector and HPI’s fully automated inspection system provides an accurate, reliable, time- and cost-efficient solution.
HPI configured its own application software for this solution, essentially integrating the NORTEC 600 unit as a sensor. The NORTEC 600 device was specifically selected by HPI over other eddy current flaw detectors as the instrument offers an interface to communicate with a programmable logic controller (PLC).
The system automatically performs calibration checks for each plate before and after the conductivity measurement. Because of its high-speed capacity, hundreds of points that would manually take many hours to measure are measured in mere minutes.
HPI’s customer uses two of these systems with two NORTEC 600 flaw detectors on each. As a quality control process, the conductivity quality check has helped to improve HPI’s heat treatment process and increase their customer’s satisfaction.
About the NORTEC 600 Eddy Current Flaw Detector
The NORTEC 600 eddy current flaw detector is a portable device incorporating advanced high-performance digital circuitry.

Easy Integration into High-Speed Automated Systems
The NORTEC 600 unit merges easily and seamlessly into integrated inspection systems. It’s built to perform consistently in industrial environments. The NORTEC 600 specifications and functionalities were designed with integrators such as HPI in mind.
- Designed to meet the requirements of IP66
- −10°C to 50°C (14 °F to 122 °F) operating temperature range
- Continuous null filter
- Strip chart view with sweep alarm
- 6 kHz measurement rate
- Remote control via NORTEC PC software
- Alarm outputs
- Analog outputs
- Digital inputs
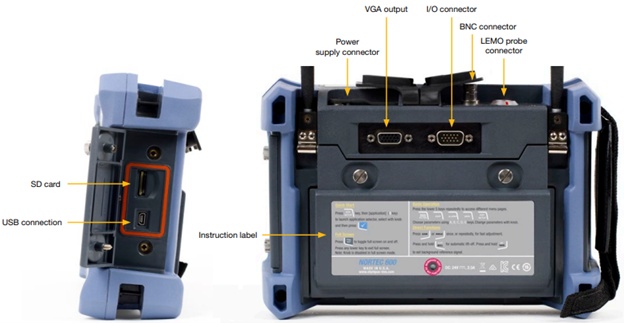
NDT Equipment for Quality Control
HPI selected to integrate the Olympus NORTEC 600 eddy current flaw detector into its automated NDT solution as it provided rapid and reliable conductivity measurement without touching the surface of the material. HPI has a long history as an Olympus integration partner—visit its product portfolio here to learn more.
Note: The following Olympus products were used in collaboration with the HPI eddy current inspection system:
- NORTEC 600C eddy current flaw detector
- Probe (9222282) with a 15.75 mm (0.62 in.) diameter; 100–500 kHz
- Cable (9122083)
Related Content
Aerospace Inspections Solutions
Get In Touch