Technical products in many industries require a certain level of cleanliness. Contamination from undesired particulates and residues in manufacturing facilities, laboratories, and on the surface of technical products can reduce product lifespans, lead to poor product performance, and generate risks in product applications.
These risks have led to the implementation of cleanliness standards in multiple industries, including:
- Automotive and electric vehicle manufacturing
- Aerospace
- Medical device manufacturing
- Electric energy supply (e.g., solar panel manufacturers and operators of wind energy converters)
Disposable medical devices, such as syringes, filters, or containers for pharmaceutical products must also be manufactured according to strict cleanliness standards. Installing a regular technical cleanliness inspection system is a crucial step to monitor the cleanliness of a production environment to avoid downtime, material loss, and energy waste.
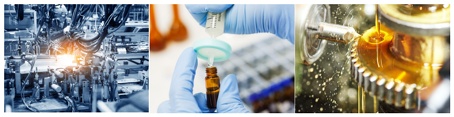
Automotive, aerospace, electrical engineering, and medical device manufacturing industries require clean production conditions and components
In this post, we introduce the first step of the technical cleanliness inspection: sampling. Read on to learn how this step fits into the overall inspection process and discover common types of sampling techniques.
An Overview of the Sampling Workflow in Technical Cleanliness Inspection
The common workflow for a cleanliness analysis starts with a random selection of technical parts from production to perform sampling. The goal of the sampling step is to collect micro particulate contamination for analysis.
In the sampling workflow, the first step is to separate contaminants from the component. Various methods can be used to extract the particulate contaminants. Selecting the extraction and sampling methods depends on the specific application and industry.
Types of Sampling Techniques for Technical Cleanliness Inspection
The following table lists the main application areas of technical cleanliness and the preferred sampling method for each one.
Application Areas | Preferred Sampling Method |
---|---|
Automotive, aerospace, medical | Washing method |
Fluids, such as oil | Direct liquid filtration |
Sensitive surfaces | Tape lift sampling |
Environment, logistics, and assembly equipment | Particle trap |
Typical sampling methods for cleanliness inspection applications
Washing parts and collecting impurities on the filter membrane is the most used process for technical cleanliness sampling. However, other methods for sampling surfaces to determine the presence of particulate contamination have been used in accordance with the analysis area of interest and the application. Tape lift sampling is a good example of a rapid and simple technique to collect particles from an accessible external part surface. It is often used in the aerospace industry.
Depending on the application, various sample holders can be used to mount samples such as a filter membrane, particle trap, and tape lift. The following list summarizes the different sample types supported by our OLYMPUS CIX100 technical cleanliness system.
Sample Holder | Application | Sample Type | Relevant Cleanliness Standard |
---|---|---|---|
Filter holder for a 25 mm diameter filter membrane with a black background |
| Foamed membrane material: cellulose nitrate or cellulose acetate |
|
Filter holder for a 47 mm diameter filter membrane with a black background |
Material: nylon (polyamide), polycarbonate, or polytetrafluorethylene (PTFE)
Size: circular with a diameter of 25 mm, 47 mm, or 55 mm Color: white or black | ||
Filter holder for a 25 mm diameter filter membrane with a white background |
These holders are good choice for a mesh filter if no aggressive solvent was used. |
Mesh filter material: PET (polyester) or nylon (polyamide)
Size: circular with a diameter of 25 mm, 47 mm, or 55 mm Color: white or yellow |
|
Tape lift holder for 50 mm and 19 mm wide adhesive tape rolls |
|
Tape lift material: polyethylene with glue Size: adhesive tape on 50 mm and 19 mm wide plastic roll (3M Nr. 480)
Color: transparent |
|
Holder for 47 mm particle traps in a 50 mm diameter Petri dish |
|
Particle trap material: foam membrane with glue on it packed in a Petri dish and stuck to a leaflet
Size: circular with a diameter of 47 mm Color: white |
|
Cleanliness Inspection Steps after Sampling
Once the sample is mounted on the microscope stage, the next step is to analyze the impurities and particles on the sample. This microscopic analysis detects and classifies the particles based on the international cleanliness standards. The results of the cleanliness inspection are presented in a report containing particle information, such as:
- Shape characteristics
- Size distribution
- Contamination level for each particle class
- Type of particle to distinguish:
- Fibers and non-fibers
- Metallic and nonmetallic particles

Standard process for cleanliness inspection
Paying Special Attention to Metallic Particles
Detecting metallic particles is crucial in many cleanliness applications as these harder particles can have drastic effects on mechanical and electrical properties.
Metallic particles do not burn in combustion engines, and exposure to them over time reduces the lifespan of components. Also, due to the high electrical conductivity of metallic materials, existence of metallic particles in the production of electrical vehicle batteries risks battery failure as they can cause a short circuit. Further, detecting metallic particles has become increasingly important as more drivers adopt electrical vehicles.
These examples show why it's necessary to distinguish between metallic and nonmetallic particles during a contamination analysis. Learn how to confirm metallic particles by reading our blog post, See Particle Contamination in Real Color to Verify Metallic Particles.
What’s Next—Learn More about Sampling Techniques in Upcoming Posts
Look out for future posts where we’ll focus on each of the common sampling methods for technical cleanliness inspections in detail, including unique applications and challenges. For more details about the basics of technical cleanliness, the most common standards used, and our CIX100 technical cleanliness system, check out our online resources or reach out to us with questions.
Related Content
Explanation of Technical Cleanliness Standards
Perform an Efficient Cleanliness Analysis with 3 Added Capabilities